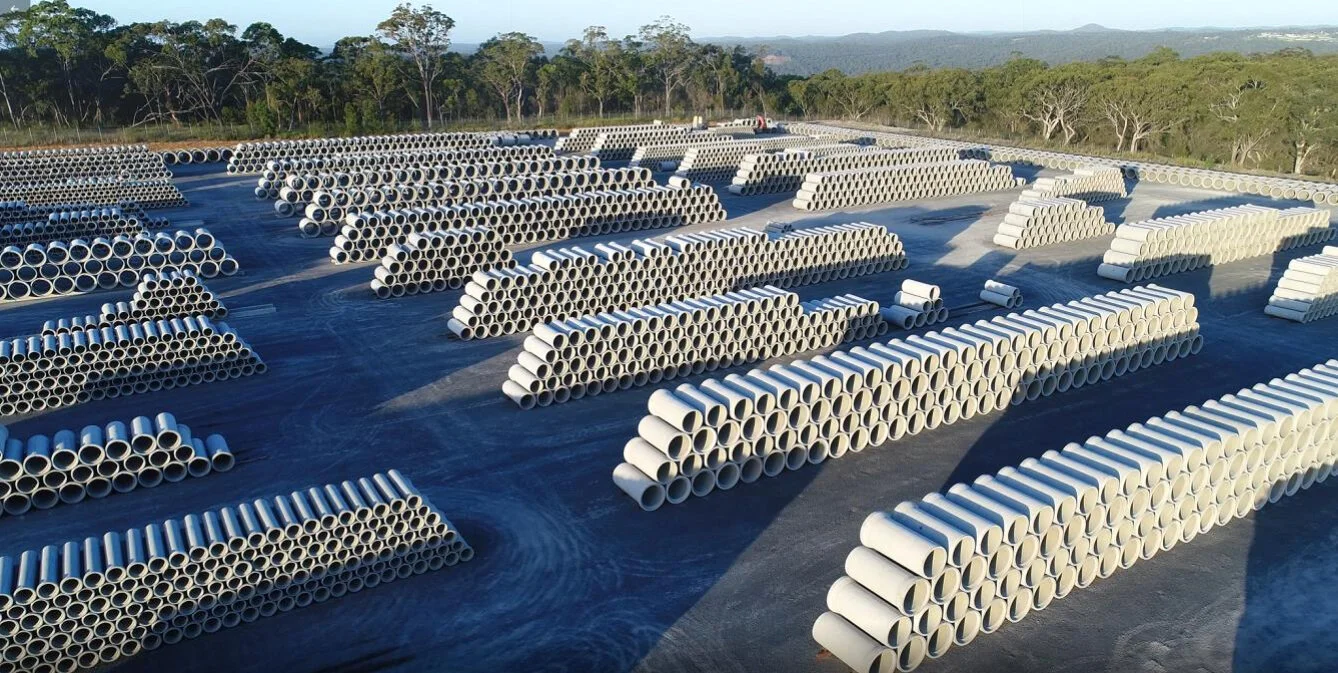
SRCPipes
Key Features and Benefits
Manufacture
Vertical cast process successfully used for over 50 years.
Pipe performance exceeds requirements of AS4058.
Continuous reinforcement cage through spigot and socket.
Cage spacers minimized to reduce ingress paths.
Dry-cast concrete with low water-cement ratio.
Durable and highly compacted with low sorptivity and carbonation rates.
Bi-directional trowels and rollers provide hard, high quality internal surface.
Non-slip exterior surface for safe handling.
Supply
Process suited to rapid and mass production providing reduced lead times.
Environmental
Efficient use of materials and little wastage.
No slurry waste.
Produced using locally sourced materials with low energy inputs.
Product Documents
Our Process
RCPA’s vertically cast concrete pipe manufacturing process begins with a cage placed in the steel mould. The assembled mould is placed on a turntable and rotated into position beneath the bi-directional compaction head. Concrete is batched on site and fed directly into the pipe machine. Concrete compaction is achieved using counter-rotating rollers and steel finishing trowels which produce an accurate and straight bore with a high quality finish. Compaction is continuously monitored for consistency.
Cage positioners ensure correct alignment of the reinforcing cage within the pipe wall. Every spigot is made using the same machined former which ensures that all spigots are identical. The one piece spigot former eliminates the traditional problems with rough grout feathering at joints. Once cast the pipe is immediately stripped and placed onto the production floor. After curing, the pipes are inspected, branded, and delivered to the stock yard.
Concrete
RCPA produces concrete in fully automated batch plants that incorporates world-class moisture sensing and correction technology. This method ensures consistent concrete of the highest standard and a product which is extremely durable. The concrete mix is specially designed for the process and uses a very low water to cement ratio, also known as zero slump concrete, which permits instant de-moulding. Test results indicate typical compressive strengths in excess of 50MPa. General purpose cement is typically used, however specialty cements can be used for specific applications if required.
Steel Reinforced
RCPA steel reinforced concrete pipes exceed market standards. Australian thin walled concrete pipes leave little room for error in cover requirement, therefore RCPA wall thickness is deliberately designed to give more than adequate cover. RCPA pipe wall thickness are deliberately designed to provide cover to steel in access of the 10mm AS4058 requirement. This provides enhanced steel protection, therefore increasing pipe durability. A continuously welded reinforcement cage (including socket and spigot) is fabricated to fine tolerances. The cover is precisely maintained by form-mounted pneumatic cage positioners that minimise the need for plastic/steel spacers. To confirm the cover, pipes are routinely tested physically and with a cover meter.